Day 2 :
Keynote Forum
Kadir Aydin
Çukurova University
Keynote: Improvement of the Heat and Sound Insulation of a Bus for Compliance with American Regulations
Time : 10:15-10:50

Biography:
Kadir Aydin received his B.Sc. degree in 1983 and M.Sc. degree in 1986 from the Mechanical Engineering Department of Cukurova University. He completed his Ph.D. degree in 1993 at the Department of Mechanical Engineering of Liverpool University. He became Assistant Professor in 1993, Associate Professor in 1995 and Professor in 2001 in the Mechanical Engineering Department of Cukurova University. He is Chairman of Automotive Engineering Department of Cukurova University and also General Manager of Cukurova Technopark. His special research areas are Internal Combustion Engines, Vehicle Technology, Combustion, Hydrogen and Electric Powered Vehicles, Alternative Fuels (Biodiesel, Bioethanol and Biogas). He published more than 150 national and international scientific papers.
Abstract:
In this study, heat, noise and vibrations of 3-axle bus which was produced according to the American regulations were determined. Insulation designs were made according to heat levels, intensity of noise and vibration and frequency. Comfort conditions inside the bus and the American regulations outside the bus were provided. Heat sources of the bus were detected. Insulations which are able to prevent the heat generated by those sources to reach passenger cabin and other badly affected areas. Maps of noise and vibration of bus is determined, according to the intensity, wavelength and frequency of the noise, using these data more insulation designs were made to reach more comfortable and quieter bus.
- Hybrid, Plug-in Hybrid and Electric Vehicles, Business Aspects of Automotive Industry, Environmental Implications of Automobiles, Fuel Economy and Emissions, Engine and Transmission Technologies, Manufacturing Technologies and Testing, Assisted and Automated Driving
Location: Meliá Valencia

Chair
Dr. Kadir Aydin
Çukurova University

Co-Chair
Dr. Lara Carlson
University of New England
Session Introduction
Gregor GregorÄiÄ
qpunkt GmbH, Austria
Title: Thermal Management in Electric and Hybrid Vehicles
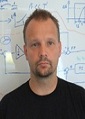
Biography:
Gregor GregorÄiÄ received the degree in electrical engineering and computer science from the University of Maribor, Slovenia, in 1998 and the Ph.D. degree in electrical engineering from the University College Cork, Cork, Ireland, in 2004. At present, he is a team leader of the Modelling and Advanced Control Group at qpunkt in Graz, Austria. His research area covers model-based predictive control systems, system identification as well as applications of local model networks and neuro/fuzzy systems for nonlinear modeling and control. His current research is concentrated on development of advanced control strategies applied to complex thermal systems in the automotive industry.
Abstract:
Rapid increase of electrification in vehicles requires batteries which are sensitive to temperature change. In order to increase a lifetime and the efficiency, the battery needs to operate at well-defined temperature levels. In comparison with a battery, the electric motor operates at different temperature level and the power electronics operates at another temperature level. The temperature and the humidity in the passenger cabin must assure a high level of comfort. This requires an air-conditioning system, which again operates at different temperature level. Multiple levels of operational temperatures require an effective thermal management of the overall vehicle. The thermal management must also assure that components operate at high efficiency, which provides the best trade-off between the mileage and the passenger comfort. Since thermal processes are nonlinear in nature, the thermal management is a complex process. To cope with nonlinearities and the complexity, advanced model based predictive paradigms must be utilised. In this talk, the advanced approaches used in thermal management will be presented. The nonlinear control of some of components will be shown and the optimisation techniques for increase of energy efficiency of thermal cycles in electric and hybrid vehicles will be discussed.
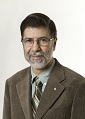
Biography:
Hussein Mouftah is a Senior Canada Research Chair Professor since 2002, and a University Distinguished Professor since 2006 at the School of Electrical Engineering and Computer Science of the University of Ottawa. He has been with the ECE Dept. at Queen's University (1979-2002), where he was prior to his departure a Full Professor and the Department Associate Head. He has six years of industrial experience mainly at Bell Northern Research of Ottawa. He has published extensively and was the recipient of several Best Paper awards and numerous prestigious career achievements awards. Dr. Mouftah is a FIEEE, FRSC, FCAE and FEIC.
Abstract:
Smart Grids and Intelligent Transportation Systems would be the main infrastructures within Smart Cities. At the same time, Plug-In Electric Vehicles (PEVs) are expected to be widely adopted as passenger cars and as commercial vehicle fleets in these smart cities since they have low carbon emissions and low operating costs. However PEVs pose a number of challenges to the smart grid due to their heavy charging load while vehicle batteries emerge as promising Distributed Energy Resources that can be used for the benefit of the smart grid. Challenges and opportunities emerging from electric vehicle integration to the smart grid brought forward numerous recent works that address architectures, models and networks to enable communications and control for electric vehicles. Electric vehicle and smart grid interaction is a newly flourishing research field receiving significant attention from communications, power and automotive societies. In this talk we will present a comprehensive background on the subject matter, present state-of-the-art architectures, models and networks in the domain and provide a thorough list of open issues which is invaluable for the researchers who are planning to steer their research direction to this area as well as expert researchers who are already actively working on this topic and seeking new directions.
Sungwha Hong
Sungkyunkwan University, Korea
Title: Development of a Mode Shift Control Algorithm for a Dual Mode Power Split Type Hybrid Electric Vehicle with On/Off Type Clutch and Brake
Time : 11:00 - 11:20
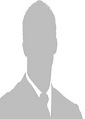
Biography:
Sungwha Hong has completed his bachelor degree in mechanical engineering from Sungkyunkwan University, Korea in 2011. He is currently working toward the Ph. D. degree at Sungkyunkwan University. His research interests include modeling, design and control of the powertrain system for the hybrid electric vehicle and electric vehicle. Hyunsoo Kim* received his Ph.D. degree in mechanical engineering from University of Texas at Austin, Texas, USA in 1986. Since 1986, he has worked as a Professor, Chairman, and Dean of the College of Engineering at Sungkyunkwan University. His research interests include Plug-in Hybrid Electric Vehicle (PHEV) and Hybrid Electric Vehicle (HEV) transmission system design, shift control for PHEV and HEV.
Abstract:
This paper presents a mode shift control algorithm for a dual mode power split type hybrid electric vehicle (HEV) with on/off type clutch and brake. The investigated dual mode power split type HEV consists of an engine, two motor-generators (MG1 and MG2), two planetary gear sets, on/off type (dog type) clutch and a brake. The target dual mode HEV requires 4 mode shift: 1)electric vehicle (EV) mode to input split mode, 2)input split mode to compound split mode, 3)compound split mode to input split mode, 4)compound split mode to EV mode. To evaluate the shift performance of the HEV, dynamic models for the HEV powertrain were developed. Using the dynamic models, a mode shift performance simulator was developed and mode shift performance simulations were performed. To analyze the transient shift characteristic of the target HEV, Bondgraph models for the transient shift state from the input split mode to compound split mode were constructed and shift dynamic equations were derived. Based on the shift dynamic equations, a mode shift control algorithm which determines the demanded torque of the engine, MG1 and MG2 during the mode shift was proposed to obtain improved the shift quality (SQ). The proposed control algorithm consists of a)Engine control, b)MG1 control and b)MG2 control. Performance of the mode shift control algorithm was evaluated using the simulator. From the simulation results, it was found that the target HEV which applied the on/off type clutch and brake can satisfy the required SQ by the cooperative control of the engine, MG1 and MG2 torque.
EstefanÃa Hervás Blasco
Universitat Politècnica de València, Spain
Title: Development of a new powertrain concept based on the integration of electric generation, energy recovery and storage
Time : 11:20 - 11:40
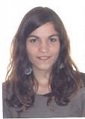
Biography:
EstefanÃa Hervás Blasco is an Engineer from the Politechnical University of Valencia (UPV). She is a PhD student (on optimization of thermal systems consumption) at the Energy Engineering Institute within a team composed by Emilio Navarro Peris (he completed his PhD in 2006, is an assistant professor at the UPV and a experienced researcher who has a great number of publications) and José Miguel Corberán (he completed his PhD in 1984, a professor at the UPV, has published several books, has a great number of contributions to the science, is the main researcher for more than 25 years, the director of the Institute and, among others, the spanish represant of different International Institutions).
Abstract:
The present concern in the reduction of C02 emissions occasioned by heavy duty trucks is leading to a technological evolution in powertrain electrification as well as to the use of cleaner fuels. Towards this objective, the EU has funded in the frame of the 7th framework program the project GASTone. This is a collaborative project between several private and public companies and institutions: CRF, FTP, Continental, GENTHERM, MAGNA and U. Politécnica de Valencia, targeting the development of a new powertrain concept based on the integration of electric generation, energy recovery and storage with engine system and control strategies The main features of this beltless engine concept are: - The energy recovery from the exhaust gases heat with a cascade approach thanks to the adoption of an advanced thermoelectric generator and a turbo-generator. - The integration of a smart kinetic energy recovery system to substitute the alternator and generate electricity during decelerations. - The electrification of the main auxiliaries by using the produced electric energy. The current average performance in a Natural Engine is about 38%; with this new concept is expected to rise this number by 4% thanks to the engine improvement, by 1% due to the modification of the liquid charge air cooler, by 2% from the reduction of the belt drive and gear losses, by 1% from the system strategy and management optimization and by 7% from the exhaust heat recovery (thermo-electric generator and turbo-generator).
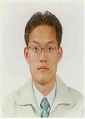
Biography:
Kwangki Jeon has completed his PhD from Seoul National University (School of Mechanical and Aerospace Engineering) of Repulic of Korea in 2013. He is the senior reseacher of Korea Automotive Technology Institute(KATECH), a chassis platform R&D center organization. He has published 7 papers in reputed journals. His research interests are vehicle dynamics, vehicle control and intelligent chassis systems.
Abstract:
Limited natural resources and environmental problems have led to increasing interest in eco-friendly vehicles such as hybrid electric vehicles, fuel cell electric vehicles(FCEVs), and pure electric vehicles. Regenerative braking in a traction motor which generates electric energy and saves it in a battery in braking situations, enhances the energy efficiency of those eco-friendly vehicles. For cooperating with the fast regenerative braking system, brake-by-wire(BBW) systems could be reasonable substitutes for the current slow hydraulic brake systems due to their fast and accurate response. Advances in design and control technologies of BBW systems have enabled the introduction of such systems, which could potentially be commercialized as replacements for current hydraulic brake systems in the near future. Because passenger safety directly depends on the functional safety and reliability of a brake system and the failure modes that may occur in a BBW system differ from those experienced in conventional brake systems such as hydraulic or pneumatic braking, a large variety of fail-safe, fault-tolerant, and fault detection methods have been developed to enhance the safety and robustness of BBW systems. In previous work, we proposed brake safety evaluation index(E-BSI1) as a quantitative metric for evaluating the fail-safe control strategies of a BBW system. E-BSI1 is the combination of a longitudinal deceleration deviation term and a lateral deviation term of the vehicle in a braking situation. In the present study, we propose a new fail-safe control strategy for one BBW actuator failure case using a new brake safety evaluation index(E-BSI2) and response surface method. The E-BSI2 is the combination of a longitudinal deceleration deviation term and yaw rate ratio term of a vehicle in straight braking situations. The proposed E-BSI2 is used as an objective (cost) function in the response surface method for designing the optimal braking force re-distribution for one BBW actuator failure case.
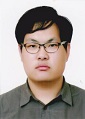
Biography:
Ji in Park has completed his B.S. and M.S. degrees in mechanical engineering from Seoul National University. He is a research engineer of Chassis Platform Center of Korea Automotive Technology Institute (KATECH). His research interests are vehicle stability control, BBW system, ADAS system and electronic power steering system.
Abstract:
At present, a hydraulic power steering system is largely used in heavy-duty vehicles. The main problem of this system, however, is that energy loss occurs mostly in straight-line driving situations (few or no steering situation), so a number of studies have researched about an application of electronic power steering system to commercial vehicles. In this paper, we introduce the dynamic model and control strategy of the Hybrid Electro Power Steering (Hybrid EPS) system which combines the Motor Driven Power Steering system (MDPS) and the Electro Hydraulic Power Steering system (EHPS). In order to integrate the control logic of MDPS and EHPS, the input and output variables of these control logics should be same. To harmonize these two control rules, we establish the model of the additional assist-boost map that defines the relationship between the assist-steering torque and the EHPS-pump-rotation speed based on the simulation model established by Matlab/Simulink and TruckSim. Using the additional assist-boost map, the integrated control strategy is designed to determine the total magnitude of the assistant steering torque and to distribute the assistant torque to the MDPS and EHPS. The dynamic model and cotnrol logic of Hybrid EPS is consistent with the test data of the conventional heavy-duty vehicle. This approach can be applied to design the optimal control logic for minimizing the energy consumption of Hybrid EPS.
Diego A. Ballén-Daza
University of São Paulo, Brazil
Title: Design and CFD analysis of a high downforce rear wing in a Formula SAE racing car
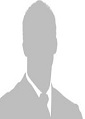
Biography:
Diego A. Ballén-Daza completed his undergraduate in Physics at the age of 26 years from Industrial University of Santander, in Colombia, obtaining Laureate Undergraduate Project for his final research project. Then, he traveled to Brazil to start a Master degree in the University of São Paulo, where currently is finishing a research in aerodynamics of racing cars. He is the head of Aerodynamics department of the EESC-USP Formula SAE Team in the University of Paulo. He has published 4 articles about fluid motion in astrophysics.
Abstract:
A design and analysis in CFD of a rear wing that generates high downforce is presented. Its dimensions are set up under the 2015 rules of the Formula SAE World Championship. Most circuits of this competition are characterized by sharp and accentuated curves demanding a vehicle with special ability for turning as fast as possible. In order to obtain high performance, is necessary a car with a special aerodynamic package that creates high downforce to generate sufficient grip between the tires and asphalt of the track. Until 2014 the aerodynamics dimensions was not strongly regulated, permitting to create aerodynamic devices with large frontal areas to obtain high downforce. Now, the 2015 regulations constrain the size of the wings, avoiding the implementation of wings with these characteristics. The main idea in our work is to show a way of recovering the downforce lost by decreasing of size, through optimization of the lift coefficient using different strategies, like creation of a special aerodynamic profile, optimization positioning, implementation of Gurney flap, vortex generators, beam wing and slats, among others. In addition, are described all of geometric and physical parameters used in a CFD simulation, and a general analysis with the overall results found.
Arjun Jamedar
Vignana Bharathi Institute of Technology, India
Title: R.A.W. car (Road, Air, Water Car)
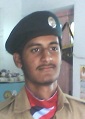
Biography:
Arjun Jamedar was born on 3/10/1995 and completed his schooling at ‘Stanley model school’ in year 2011. At his schooling itself he has got a state level prize for his paper presentation. Now, am doing his graduation (engineering) at Vignana Bharathi Institute of Technology. Representing the college, he went to national level competition IFAST-2015 and got national award and reward for his model R.A.W. car.
Abstract:
The name of the project is RAW car. It means a car which moves on Road, Air, and Water. This car is very useful for defense purpose and for the cops to catch the criminals. A criminal can escape by any way, by using any means of transport. So this car is useful to catch them. This car is made, such that it can move from road to air, air to water, road to water, water to air, water to road, air to road. Impact on society: This car will have a greater impact in the Defense field. R.A.W. Car can be used to help people who are stuck in regions where normal helicopters or cars cannot go. The car which has been designed is of two different types. Type (1): • A motor for both Road, Water motion. • A motor for Air motion. Type (2): • A motor for all Road, Air, Water motion. In type one, the car normally looks like the other cars which we see on roads and have the same motion on road with the same engine but for the movement on water, there are some design changes to wheels. So that it can float on water and have its motion. For flying in the air, a quadcopter has been utilized. In type (2) car, utilizing a quadcopter all three motions has been tested. In practical, we can use the type (1) car as it uses petrol (if made big), and white petrol to fly in necessary time. Coming to type (2), which runs completely on quadcopter, it uses white petrol to for motion. Keeping the cost into account, type (1) car has been designed.
EstefanÃa Hervás Blasco
Universitat Politècnica de València, Spain
Title: Model of a new powertrain concept based on the integration of electric generation, energy recovery and storage
Time : 14:50 – 15:10
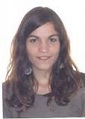
Biography:
EstefanÃa Hervás Blasco is an Engineer from the Politechnical University of Valencia (UPV). She is a PhD student (on optimization of thermal systems consumption) at the Energy Engineering Institute within a team composed by Emilio Navarro Peris (he completed his PhD in 2006, is an assistant professor at the UPV and an experienced researcher who has a great number of publications) and José Miguel Corberán (he completed his PhD in 1984, a professor at the UPV, has published several books, has a great number of contributions to the science, is the main researcher for more than 25 years, the director of the Institute and, among others, the spanish represant of different International Institutions).
Abstract:
The growing need for a sustainable transport has brought researches a potential improvement of the engine thermal efficiency. In that line, more than 50% of the available energy from the fuel is not used in Gas Engines. In order to recover part of this energy, a global approach which integrates a combination of different alternatives to increase the system efficiency is of major relevance and in that direction the development of accurate models is crucial. In this contribution a dynamic model in order to analyze the potential of a new powertrain concept focused on the recovery of a portion of kinetic energy and waste gases heat is presented. The model analyzes the beltless engine concept based on the electrification of the main auxiliaries and the implementation of a kinetic energy recovery system and the use of the heat from exhaust gases through a thermoelectric generator and a turbo-component. The model has a modular structure allowing changes on the circuit configurations and on the present components. The model architecture makes easier the study and determination of the most suitable configurations, the optimum control of the system and the possible obtained benefits in terms of fuel saving for a target driving cycle based on European heavy duties roads, speed and torque. The global structure of the model allows anticipating the impact of every possible condition/element modification and gives the capability of analyzing the effect of the components within a whole system and not only in one part of it.
Sunyoung Park
Sungkyunkwan University, Korea
Title: A Comparative Study on Power Characteristics and Mode Control Algorithm for Plug-in Hybrid Electric Vehicles
Time : 15:10 – 15:30
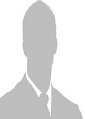
Biography:
Sunyoung Park received B.S. degree in mechanical engineering from Sungkyunkwan University, Suwon, Korea, in 2014, where she has been working toward the M.S. degree. Her research interests include the powertrain system, control strategy of electric vehicles, hybrid electric vehicles and plug-in hybrid electric vehicles. Hyunsoo Kim* received his Ph.D. degree in mechanical engineering from University of Texas at Austin, Texas, USA in 1986. Since 1986, he has worked as a Professor, Chairman, Dean of the College of Engineering and Executive Vice President at Sungkyunkwan University. His research interests include design and control of Plug-in Hybrid Electric Vehicle (PHEV) and Hybrid Electric Vehicle (HEV) transmission system.
Abstract:
In this paper, a comparative analysis was performed on power characteristics and mode control algorithm for plug-in hybrid electric vehicles (PHEVs): Honda Accord and Toyota Prius+. The power characteristic analysis of the target PHEVs was conducted to obtain the operating range of the possible vehicle velocity and driveshaft torque for each driving mode such as EV, HEV mode and Series mode. For each mode, the system efficiency was calculated by considering the powertrain component(motor, generator, engine, planetary gear set and clutch) efficiency and vehicle driving condition such as vehicle velocity and driveshaft torque since the powertrain component efficiency changes depending on the vehicle driving condition. Using the calculated system efficiency, a mode shift map was developed for each driving mode. Based on the developed mode shift map, the mode control algorithm was proposed to obtain the improved system efficiency. The vehicle performance simulator and control algorithm such as regenerative braking control and engine optimal operating line control were developed for target PHEVs. The proposed mode control algorithm was applied to each target PHEVs. Through the simulation results, a comparative analysis was performed on the power characteristics and mode control algorithm for the target PHEVs. This comparative analysis can be used to design the power-split PHEV configuration and to develop the optimal mode change algorithm.
Ali Shaeri
NIOEC, Iran
Title: Simulation the Continuous Catalytic Reforming (Octanizer) Unit of Arak Refinery Gasoline Production Complex with PETROSIM Software
Time : 15:30 – 15:50
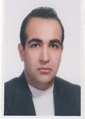
Biography:
Ali shaeri is a student in PhD (Passed General Exam) and working in NIOEC as a senior process engineer. He is member of IPS and teaching in the university and member of a Scientific Mission in Elmi- Karbordi University. He was responsible for commissioning and pre-commissioning of process units in Arak Refinery Expansion Project.
Abstract:
Naphtha catalytic reforming is one of the most important and key processes in any refineries. In this process, mainly gasoline is produced with high octane number and in petrochemical complexes expensive Aromatics such as benzene, toluene and xylene are also produced. Consideringin creasing need and the importance of quality and quantity of desirable gasoline , it is necessary to simulate the process of naphtha catalytic reforming to achieve the best values of operational variables , enforcing the best solution in dealing with fluctuations and changes in processing conditions, identification and removing bottlenecks , reducing production costs by the simulation of above mentioned process. In this research, firstly the processes leading to the production of high octane gasoline in the naphtha catalytic reforming are explained with continuous catalyst regeneration unit of Esfahan oil refinery then has been stimulated by PETROSIM software.
Hasan AydoÄŸan
Selçuk Üniversitesi, Turkey
Title: An Experimental Study of the Effects of Camelina Biodiesel on Engine Emissions
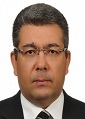
Biography:
Hasan AydoÄŸan is a PhD in engineering department. His major is renewable energy and biodiesel. Currently he is appointed as an Assist. Prof. Dr. in the Mechanical Engineering Department program of the Technology Faculty of Selcuk University.
Abstract:
Being one of the most primary inputs of everyday life and the industrial world, energy has been used in various ways since the first existence of human beings. When we look at the types of energy used today, we can see that the mainly used types of fuels are fossil based. CO2 is emitted as a result of the combustion of fossil-based fuels. The increasing amounts of CO2 in the atmosphere create a greenhouse effect. Biofuels have been becoming prevalent rapidly because of constantly gaining economic value and concordantly having less negative effects on the environment. All plant and animal based substances with carbohydrate compounds as main components are biofuel resources. This study includes an examination of the different kinds of biofuels and their effects regarding environmental-related aspects.
Abhik Rathod
VIT University, India
Title: Evaluation of properties for Hybrid Al-SiC-Carbon Fiber Reinforced Metal Matrix Composite for Brake Pads
Time : 15:50 – 16:10
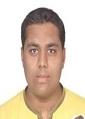
Biography:
Abhik Rathod has completed his B.Tech at the age of 21 years from Gujarat Technological University in June 2012 and M.Tech from VIT University, Vellore in May 2015. Currently he is an Intern at Volvo India Pvt. Ltd. (VIPL) Bangalore. He has presented 1 research papers in international conference Global Congress on Manufacturing and Management (GCMM 2014) held on 8-10 December, 2014 at VIT University, Vellore and published 2 research papers in reputed journals. He has participated in Summer School on Automotive Manufacturing and management held on 21st July 2014 to 1st August 2014 at Technische Hochschule Ingolstadt (THI), Germany.
Abstract:
In engineering application MMC is playing vital role due to its mechanical and physical properties. In automobile sector they are mainly used due to its high strength to weight ratio, light weight, low cost and good behavior. The aim of this research is to develop carbon fiber and SiC reinforced hybrid Aluminium metal matrix composite for automotive brake pad application. In present study the mechanical and wear behavior of hybrid Aluminium metal matrix composite reinforced with SiC and carbon fiber with five different formulation of varying carbon fiber content by 0.5, 0.6, 0.7, 0.8 and 0.9 volume fraction along with fixed content of SiC(20%) reinforcement has been discussed. Brake pad is manufactured via route of powder metallurgy which is widely preferred due to its low cost, high volume production, ease of operation, sustainability and attractive manufacturing process. Also brake pads are developed with hybrid composite (Light alloy Aluminium 6061 reinforced with SiC and carbon fiber (3K Grade of 0.5mm)) to augment the strength and wear resistance and explore the advantage of low density of the matrix.
Ibrahim Yahuza
Abubakar Tafawa Balewa University, Nigeria
Title: A Review of Ethanol-Diesel Blend as a Fuel in Compression-Ignition Engine
Time : 16:10 – 16:30
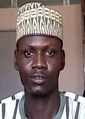
Biography:
I. Yahuza has completed his M.Eng. at the age of 29 years from Abubakar Tafawa Balewa University, Bauchi Nigeria. He is the Examination Officer of the Department of Automobile Engineering, Abubakar Tafawa Balewa University, Bauchi Nigeria. He has published 5 papers in reputable journals. H. Dandakouta has completed his PhD at the age of 31 years from Abubakar Tafawa Balewa University, Bauchi Nigeria. He is the Coordinator of Postgraduate Studies of the Department of Mechanical/Production Engineering, Abubakar Tafawa Balewa University, Bauchi Nigeria. He has published more than 30 papers in reputable journals and has been serving as an editorial board member of Ahmadu Bello University, Zaria, Nigeria.
Abstract:
Ethanol was produced from saw dust of Masonia wood by means of simultaneous saccharification and fermentation process. The Ethanol produced was blended with Diesel in different proportions. The fuel properties of the Ethanol-Diesel (ED) blends at different temperatures and load conditions were experimentally investigated. The properties determined were relative density, cloud point, pour point, flash point, viscosity and the calorific value. The Diesel Engine Test Bed (Petter: PJ2W-type, 7227/22.5 BS) was used with ED blends having 5, 10, 15 and 20% ethanol with respectively 95, 90, 85 and 80% diesel on a volume basis to know the performance of the blends. The experimental results of the engine’s performance which include the brake power, brake specific fuel consumption, brake thermal efficiency for the fuel blends were analyzed to know the suitability of using ED blend in Compression Ignition engine. The results show that both the relative density and viscosity of the blends decreased as the ethanol content in the blends was increased. All the blends were found to have the same cloud point of 50C with that of diesel while their pour points vary and differ from that of diesel. All the blends have flash points 65% lower than that of diesel. The calorific values for ED5, ED10, ED15 and ED20 blends were 2, 3, 4 and 6% respectively less than that of diesel. The engine’s performance analysis indicated that there was an increase in brake thermal efficiency of the engine with increased proportion of ethanol in the fuel blends. The ED20 gave higher brake thermal efficiency than the diesel fuel at all load conditions. It was observed that at all loads conditions, the mass flow rate of ED20 was low so, resulting in decreased in specific fuel consumption. At all loads conditions, carbon dioxide emissions increased while hydrocarbon emissions decreased with increased amount of ethanol in the fuel blends, with ED20 showing the least emissions levels. Also, at all loads conditions, NOX emission of the blends was found to be higher than that of standard diesel due to the oxygen concentration and combustion timing. The results found showed that the ED20 (20% ethanol and 80% diesel) can be used in CI engine without any modification.
Pauline Korukundo
KIIRA Motors, Uganda
Title: Development of the KIIRA EV SMACK Supervisory Control Firmware
Time : 16:10 – 16:30
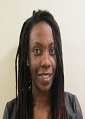
Biography:
Pauline K. is currently doing her Master’s degree in Electrical and Electronics Engineering at the University of Nottingham, UK. She obtained her BSc. in Telecommunications Engineering from Makerere University, Kampala, Uganda, 2012. She has worked on the Kiira EV Project and the Kiira Motors Project, as a Vehicle Electronics and Information Systems Researcher in Kampala, Uganda. Her interests are in control algorithms and high performance computing.
Abstract:
The growth in number and complexity of controlled electrical sub systems in the modern car has created a need for centralized control and an information interchange point. The supervisory controller provides this centralized unit. It interacts with all other networked control electronics hence controlling the dynamic driving demands. In a hybrid car, the complexity is greater because of the extra energy resources integrated into the vehicle. The supervisory controller must therefore provide efficient energy management and performance during the various vehicle specific drive cycles. This work presents the design, implementation and testing of the Kiira EV SMACK vehicle level control with key consideration of range extension capabilities of the hybrid. The Kiira EV SMACK supervisory controller oversees the human machine interfaces, low voltage electronics, the motor and generator controllers, battery management and thermal management systems. It initiates the startup of the low level controllers, implements a power source switching strategy based on speed demands and available energy resources determined by battery state of charge and fuel capacity. A model based firmware development approach was followed with utilization of the MotoHawk rapid prototyping tool built to work with MATLAB Simulink. The firmware was deployment on Woodward\\\'s 112 embedded hardware platform. The testing and verification followed hardware in the loop (HIL) testing methodology.
Daniel Uguru-Okorie
Landmark University, Nigeria
Title: Effect of Supercharging on the Combustion Characteristics of Some Selected Fuels
Time : 16:50 – 17:10
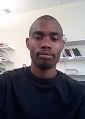
Biography:
D. C. Uguru-Okorie received a B.Eng degree in Mechanical Engineering from the Federal University of Technology, Owerri, Nigeria, a MSc. degree in Mechanical Engineering (Thermo-Fluids Option) from the University of Ibadan, Nigeria and he is currently a PhD student in the Department of Mechanical Engineering, University of Ibadan, Nigeria. He was also a visiting PhD research student in the University of Leeds, UK under the sponsorship of Petroleum Technology Development Fund (PTDF). He is currently a lecturer in the Department of Mechanical Engineering, Landmark University, Nigeria. His research interests are in the areas of Engines and Combustion.
Abstract:
Spark Ignition engines find wide applications as prime movers in light vehicles and domestic power generating units. The power output of these spark ignition engines could be improved by boosting the intake pressure and compression ratio; however the applications of these are limited by knock in engines. A reduction in cycle-to-cycle variation in engines have been noted by researchers as one of the methods of improving engine efficiency with a study showing that engine efficiency could be increased as much as 10% with a reduction in cycle-to-cycle variation. This study investigated the combustion performance characteristics of two fuels: E5 (95% gasoline and 5% ethanol) and ULG98 (unleaded gasoline) operating at varying inlet pressure conditions and ignition timing in a Spark Ignition engine. A two-stroke, 80mm bore, spark ignition engine was operated at 1.6 and 2.0 bar inlet pressures using E5 and ULG98 fuels at 750 rpm and at spark-timings of 2 and 5 bTDC. A metal top cylinder head with a centralized spark plug was used for all the experiments. The Indicated Mean Effective Pressure (IMEP), IMEP Coefficient of Variance (COVIMEP), the Crank Angle of Cycle Peak Pressure (CApmax) Occurrence and the Crank Angle of Occurrence of 10, 50 and 90 % Mass Fraction Burned (MFB) were determined. The results of the increase in engine intake pressure from 1.6 to 2.0 bar, showed an increase in engine IMEP for E5 of 20.7 and 21.5%; and for ULG 98, 24.0 and 20.2 % for 2 and 5 bTDC spark timings respectively. A reduction in the coefficient of variation of the IMEP (COVIMEP) (which is an indicator for cycle-to-cycle variability in engines) by 23.4 % and 15.8 % for E5; and 50% and 26.9% for ULG 98 at spark timings of 2 and 5bTDC respectively. For the crank angle of peak pressure occurrence (CApmax), an increase of 9.4 and 14.6 % for E5 was observed while a decrease of 1.7 and 11.4 % was observed for spark timings of 2 and 5 bTDC respectively. The crank angle of occurrence of the 10, 50 and 90% of MFB for E5 increased with an increase in the inlet pressure by 5.7, 9.9 and 9.8% at 2bTDC and 30, 15.2 and 11.2 % at 5bTDC while ULG 98 showed an increase in burning rate with an increase in inlet pressure as evident in the reduction of the crank angle of occurrence of 10, 50 and 90% MFB by 1.2, 1.7 and 1.9 % at 2bTDC and 22.8, 14.8 and 13.3 at 5bTDC The study established that a reduction in the cycle-to-cycle variation in an engine can be achieved by supercharging or turbo-charging engines; which improves the engine efficiency.